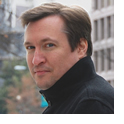
Personal Kanban: Lean Thinking for Leaders
Jim Benson, Modus Cooperandi
In Lean management, inventory is considered waste; for individuals, our backlog is our inventory. The trick is to carry just the right amount of inventory to create value, without having the overhead of keeping track of a massive catalog. Most leaders carry a seemingly infinite and ever-growing backlog of demands and obligations—and the scope and shape of their work is poorly understood.
- Leaders have commitments to staffing, vision, financials, regulators, ongoing projects, and the inevitable unexpected emergencies that eat up valuable time. Since this work is not tangible—leaders don’t build tangible objects like cars or houses—leaders may feel that others don’t understand the volume or scope of work they’re exposed to.
- For their part, leaders often don’t have an objective view of their own work. Valuable options are often left unexplored, while hours are wasted in unproductive meetings or chasing dead ends. This leads to frustration because leaders’ time is valuable and actionable information is scarce.
Personal Kanban, which is based on principles of Lean manufacturing, can help leaders with these perennial frustrations and challenges. A kanban system, such as that initiated by Toyota, uses visual tools to ensure that components arrive just in time—when they’re needed and not before—thereby preventing waste, minimizing inventory, and reducing storage costs. Personal Kanban applies those principles to the individual.
Reducing Your Backlog
Perhaps the biggest reason most leaders carry a huge backlog is that they confuse free space or free time with capacity. In saying “I have a free five minutes here, I can talk to you then,” leaders attempt to maximize value by maximizing scheduled time. This is a dangerous gambit—leaders leave themselves stretched thin—unable to relax, make good decisions, or react to those unavoidable emergencies.
It’s helpful to think of your mind as a freeway. A freeway can support between 0% and 100% capacity. But when capacity extends beyond 65%, traffic on the freeway bogs down. When a freeway reaches 100% capacity, traffic comes to a standstill. We’ve all been there—on that clogged and stagnant freeway—and yet we often treat ourselves as a freeway with infinite capacity.
Simply because a few more cars can enter the freeway does not mean it’s a good idea. Simply because you think you can handle more work-in-progress does not make it so.
Picture a freeway where traffic is clipping along; the lanes aren’t overloaded and there’s adequate space between the cars. We need that same mental space to keep our brains functioning at a high level. We need our minds to be Lean—without excess inventory—in order that our thinking can be supple, focused, sharp, and dynamic.
Limiting Work-In-Progress
So, how do you keep your mind, and therefore your thinking, Lean? There are only two steadfast rules with Personal Kanban:
- Visualize your work.
- Limit your work in progress.
We each have a personal value stream just like a supply chain has a value stream. In Personal Kanban, Tonianne DeMaria Barry and I suggest visually organizing your work by putting tasks on sticky notes and placing those notes on a whiteboard labeled with your value stream.
The simplest version of a Personal Kanban has three elements in the value stream: Backlog, Doing, and Done. Tasks then move across this simple workflow. You can always change this value stream to one that matches your personal conditions—after all it is just ink on a whiteboard.
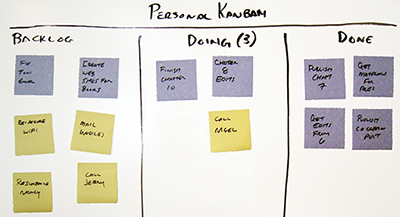
As we can see in this picture, the “Doing” column has a Work in Progress (WIP) limit of three. Items in the doing column need to be completed before a new item can begin. This limit—as clearly displayed in your kanban—has some key impacts:
- It creates an economy of time. Before the WIP limit, you could take on work with impunity. This meant there was no cost associated with taking on more work. However, just like each additional car makes the freeway slower and lowers the quality of the “product” of driving, so too does each item of work you start but do not finish. The WIP limit enforces completion, quality, and focus.
- It highlights true opportunity costs. Each item in your backlog is an option that you can choose to exercise or discard. Since we’ve now increased the value of starting a new task, we’ve also increased the degree to which we examine new options. In other words, we’ve enlivened our own work-economy and the options trading we do every day.
- It shows others true overhead and effort. This is especially valuable for leaders relating to staff. Staff members often perform knowledge work, which is invisible. Leaders, because they are busy, have little idea of the real volume of work being done by staff. This leads to hastily given direction, premature beginnings to projects, and unreasonable deadlines, all of which could be rectified if staff or teams showed their work in a kanban that their leaders could see.
It’s imperative that you establish a work-in-progress limit. That means being honest with yourself about the amount of work you can handle—that you can actively, successfully, and effectively accomplish—at one time. For most people, establishing a work-in-progress limit of three things is a good start.
Keeping in Check
Keeping your work-in-progress limited may be one of the hardest challenges you’ve ever faced as a leader. We all have a tendency to overcommit and to leave many things half-done (which, by the way, our brains hate). Part of what makes Personal Kanban so effective is that, by regulating the flow of our work, it helps us find the sweet spot where we are doing the optimal amount of work at the optimal speed.
As productivity guru and Getting Things Done author David Allen explains, “You're the one who creates speed, because you're the one who allows stuff to enter your life." Like with the flow of traffic on the freeway, we can control the speed by how many cars—how much work in progress—we let in at any given time. As a leader, if you don’t learn to manage the number of obligations you have at any one time, they will weigh on and clutter your mind, hindering your productivity.
It’s also important to keep your backlog in check. If you were successful in keeping to three items at any given time under “Doing” but then put 54 items under “Backlog,” you would likely feel defeated before even starting. Your backlog should be a set of immediately actionable options, rather than an infinite mass of ambiguous hopes and desires.
Putting Things in Their Place
Starting with three as your work-in-progress limit, put those three things in your visual organization system under “Doing” (or “Now,” “Current Work,” or whatever term you choose to represent your work in progress). And then put everything else somewhere else.
David Allen’s advice is to “get it all out of your head.” This advice reflects just-in-time production principles, as well as the rules of Personal Kanban to visualize your work (for instance, out of your head and onto paper) and to limit your work in progress (including tasks swirling around in your head).
In the end, the kanban is about visualizing policies, processes, and procedures; it’s about seeing the hard-to-manage stuff that’s been hard to manage because it’s been invisible. Once you’re able to see your work more clearly, you’ll be better equipped to stick to a strict work-in-progress limit—and keep the freeway of your mind running at optimal (rather than maximum) capacity.
Jim Benson is the CEO of Modus Cooperandi, a collaborative management consultancy, and is the author of Why Plans Fail and co-author of Personal Kanban. He has worked with small startups, Fortune 100 corporations, World Governments, and educational institutions like UW. You can learn more about Jim and his work at http://moduscooperandi.com and www.personalkanban.com.
========
SOURCES
Getting Things Done: The Art of Stress-Free Productivity by David Allen
Kanban Just-In-Time at Toyota: Management Begins at the Workplace by David John Lu, Nihon Nōritsu Kyōkai
Personal Kanban by Jim Benson & Tonianne DeMaria Barry